Foshan Carlsberg Beer Program Team Achieves Another Successful Result
Publishdate:2024-05-24 Source: Views:681
Carlsberg Beer Program Team in Foshan achieves another good result
--Carlsberg Zero Accident Leadership Award for 2 Million Safe Work Hours
Recently, our Foshan Carlsberg project team has successfully won Carlsberg's Zero Accident Leadership Award by virtue of its excellent safety management capability and continuous technical innovation. This honor is not only a high recognition of the company's technical engineering team, but also the best interpretation of the company's philosophy of always insisting on safety first and technological innovation.
The Carlsberg (Foshan) beer production base project will start construction in 2022, with a total investment of 3 billion yuan, an annual output value of about 2 billion yuan, and a production capacity of 500,000 kiloliters, with the most advanced technological standards, intelligent manufacturing and ESG, and the flagship brewery will be the first of its kind for the Carlsberg Group in the world.
It is worth noting that the winery will become the first "sponge winery" of Carlsberg Group in the world, which consists of four large underground cisterns with a total volume of 3,000 cubic meters of rainwater collection and treatment system, realizing the recycling of rainwater, conserving freshwater resources and reducing wastewater discharges. Photovoltaic panels are installed over a large area, with a total installed capacity of about 6 MW, and advanced energy storage equipment is installed to meet 20%-30% of the plant's production power consumption. Intelligent monitoring and management systems will reach the shop-floor equipment level to monitor and control the energy consumption of the entire plant in real time, enabling optimized energy use and helping the management team to fully explore the potential for energy savings. The new R&D center is Carlsberg's first R&D center outside of Europe, providing new product development, package design and testing services for the Chinese and Asian markets.
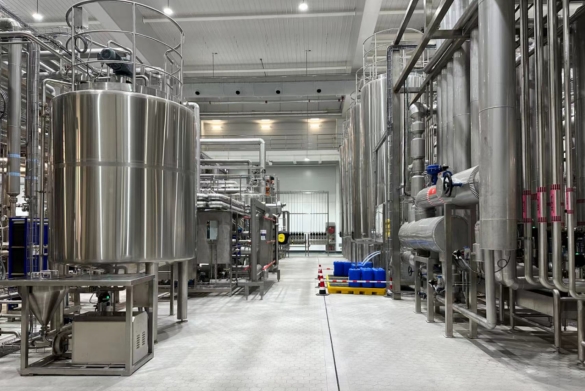
As a key project of Ology in recent years, the Carlsberg project team in Foshan is not only excellent in terms of technological breakthroughs, but also in terms of safety management, which is a top priority. "Connection" is the core keyword of the whole project:
The beer processing room is the centerpiece of the project, connecting the three sections of the cold zone, the hot zone and the packaging;
The pipeline is the core of the project, connecting the media transport between the various systems and realizing the barrier-free and controlled transmission of substances over long distances;
The basis for the unobstructed and controllable transmission is the switching and control of a large number of valves, the linkage of the power supply of the pumping units and the real-time monitoring of the instrumentation.
As a result, the pipeline network and the electrical network are jointly constructed, the electrical network provides power and monitoring for the pipeline network, and the pipeline network provides feedback and real-time data for the electrical network, which further improves the intelligent control.
Safety as a red line has always been the top priority in the site management of Ology project, and it is also the core concept of Carlsberg, and the double emphasis of both parties will undoubtedly integrate the concept of safe construction into everyone's mind. As an Ology person, the project team always remembers the construction principle of "safety first, prevention first", strictly implements the responsibility system of safety construction, formulates safety management measures and establishes a perfect safety management system.
The existence of risk is unavoidable, the strategy and method to deal with risk is the project team's management personnel must be taken seriously, for this reason, the project team's daily safety morning meeting to emphasize the construction safety, special safety training, safe operation of work equipment training cycle intermittently emphasized. Hollow multi-storey span galvanized pipe gallery in the case of not allowed to weld the pipe card directly in the support column beams, the need for welding and bracket which undoubtedly raises the risk of operational safety, rainy Foshan and for the use of outdoor temporary electricity put forward higher requirements. In order to solve these problems, the project team in the corridor construction European standard scaffolding set up a special up and down channel, corridor top assumption of 12mm steel cable lifeline, corridor span and span between the use of springboards and fixed, the work tool is placed with the toolkit to put the fall, up and down the process of the whole process must wear a seatbelt and do not allow off the hook. And in the pipeline corridor construction, steam pipe installation is the focus of safety management, due to the carbon steel pipe long and heavy, need to install with the help of cranes, and construction of the ground cause lifting point location is far away, lifting process command and communication, lifting area isolation guardianship need to pay attention to all the time. In the process of steam pipeline installation, the project team implemented the crane driver with command, double certificates, lifting area to prevent other personnel from entering by mistake, pipeline in the pipe gallery using tooling for accurate piping; and fermentation irrigation area as an important part of beer production, this part of the construction also exists in a number of potential safety hazards, especially in the flagship plant to join the innovative fermentation process, the first time to contact with the project team has a certain challenge, in order to cope with the risks, the project team has a lot to do. In order to cope with the risks, the project team provided special training to the personnel of the lift trucks, and wrapped the lift trucks around with rubberized cotton to prevent collisions and prevent safety accidents from occurring.
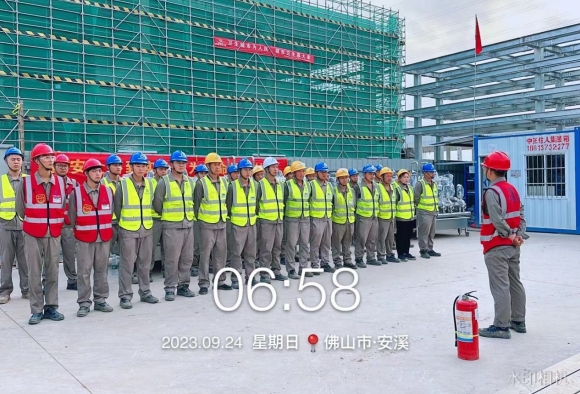
In addition to these, there are also in the use of temporary electricity in the process of power line broken rectification before use, the risk of protection of pipe corridor welding, welding equipped with a fire catching basin and in the lower layer of the fireproof cloth for protection and so on, it is these strict safety management measures and continuous improvement, so that the company in the past year to achieve the goal of zero accidents, won the recognition of the Carlsberg Zero Accident Leadership Award.
This award is the result of the joint efforts of all construction staff and the project team, and the sense of responsibility is hidden in everyone's heart. By continuously improving the safety management system, introducing advanced technology, optimizing production process and other measures, not only has the goal of zero accident been achieved, but also promotes the development of the company's technological innovation. This honor is not only a high recognition of the company's technical engineering team, but also the highest praise for the company's persistent adherence to the concept of safety first and technological innovation. Today, the Carlsberg (Foshan) Beer Production Base Project is advancing the installation of equipment and preparing for the launch of trial production, which will be officially put into operation at the end of August.
We are confident that adhering to the sustainable development path of green, low-carbon and energy-saving will make the mountains where our customers are located more beautiful, the water clearer and the sky bluer, injecting strong vitality into industrial development and becoming a new flag-bearer in promoting the high-quality development of the local economy and society.
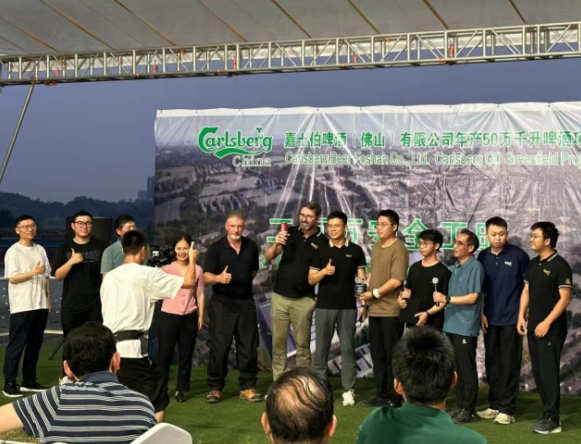
(Text/Engineering Center Chen Yangyang, Strategic Operation Department Zhang Hanlu)
Carlsberg Beer Program Team in Foshan achieves another good result
--Carlsberg Zero Accident Leadership Award for 2 Million Safe Work Hours
Recently, our Foshan Carlsberg project team has successfully won Carlsberg's Zero Accident Leadership Award by virtue of its excellent safety management capability and continuous technical innovation. This honor is not only a high recognition of the company's technical engineering team, but also the best interpretation of the company's philosophy of always insisting on safety first and technological innovation.
The Carlsberg (Foshan) beer production base project will start construction in 2022, with a total investment of 3 billion yuan, an annual output value of about 2 billion yuan, and a production capacity of 500,000 kiloliters, with the most advanced technological standards, intelligent manufacturing and ESG, and the flagship brewery will be the first of its kind for the Carlsberg Group in the world.
It is worth noting that the winery will become the first "sponge winery" of Carlsberg Group in the world, which consists of four large underground cisterns with a total volume of 3,000 cubic meters of rainwater collection and treatment system, realizing the recycling of rainwater, conserving freshwater resources and reducing wastewater discharges. Photovoltaic panels are installed over a large area, with a total installed capacity of about 6 MW, and advanced energy storage equipment is installed to meet 20%-30% of the plant's production power consumption. Intelligent monitoring and management systems will reach the shop-floor equipment level to monitor and control the energy consumption of the entire plant in real time, enabling optimized energy use and helping the management team to fully explore the potential for energy savings. The new R&D center is Carlsberg's first R&D center outside of Europe, providing new product development, package design and testing services for the Chinese and Asian markets.
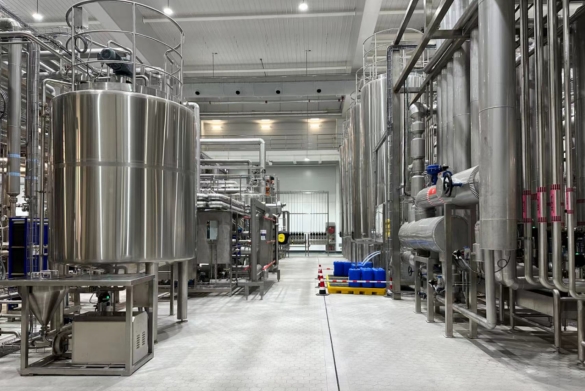
As a key project of Ology in recent years, the Carlsberg project team in Foshan is not only excellent in terms of technological breakthroughs, but also in terms of safety management, which is a top priority. "Connection" is the core keyword of the whole project:
The beer processing room is the centerpiece of the project, connecting the three sections of the cold zone, the hot zone and the packaging;
The pipeline is the core of the project, connecting the media transport between the various systems and realizing the barrier-free and controlled transmission of substances over long distances;
The basis for the unobstructed and controllable transmission is the switching and control of a large number of valves, the linkage of the power supply of the pumping units and the real-time monitoring of the instrumentation.
As a result, the pipeline network and the electrical network are jointly constructed, the electrical network provides power and monitoring for the pipeline network, and the pipeline network provides feedback and real-time data for the electrical network, which further improves the intelligent control.
Safety as a red line has always been the top priority in the site management of Ology project, and it is also the core concept of Carlsberg, and the double emphasis of both parties will undoubtedly integrate the concept of safe construction into everyone's mind. As an Ology person, the project team always remembers the construction principle of "safety first, prevention first", strictly implements the responsibility system of safety construction, formulates safety management measures and establishes a perfect safety management system.
The existence of risk is unavoidable, the strategy and method to deal with risk is the project team's management personnel must be taken seriously, for this reason, the project team's daily safety morning meeting to emphasize the construction safety, special safety training, safe operation of work equipment training cycle intermittently emphasized. Hollow multi-storey span galvanized pipe gallery in the case of not allowed to weld the pipe card directly in the support column beams, the need for welding and bracket which undoubtedly raises the risk of operational safety, rainy Foshan and for the use of outdoor temporary electricity put forward higher requirements. In order to solve these problems, the project team in the corridor construction European standard scaffolding set up a special up and down channel, corridor top assumption of 12mm steel cable lifeline, corridor span and span between the use of springboards and fixed, the work tool is placed with the toolkit to put the fall, up and down the process of the whole process must wear a seatbelt and do not allow off the hook. And in the pipeline corridor construction, steam pipe installation is the focus of safety management, due to the carbon steel pipe long and heavy, need to install with the help of cranes, and construction of the ground cause lifting point location is far away, lifting process command and communication, lifting area isolation guardianship need to pay attention to all the time. In the process of steam pipeline installation, the project team implemented the crane driver with command, double certificates, lifting area to prevent other personnel from entering by mistake, pipeline in the pipe gallery using tooling for accurate piping; and fermentation irrigation area as an important part of beer production, this part of the construction also exists in a number of potential safety hazards, especially in the flagship plant to join the innovative fermentation process, the first time to contact with the project team has a certain challenge, in order to cope with the risks, the project team has a lot to do. In order to cope with the risks, the project team provided special training to the personnel of the lift trucks, and wrapped the lift trucks around with rubberized cotton to prevent collisions and prevent safety accidents from occurring.
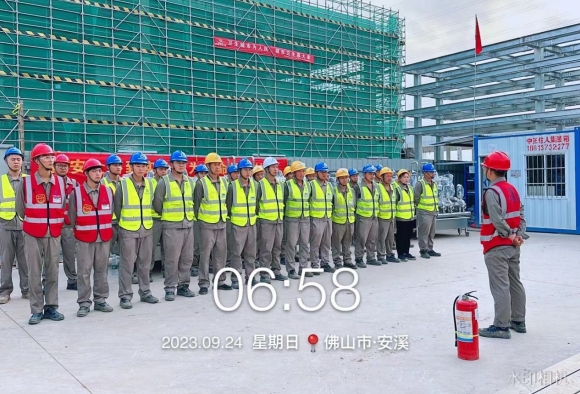
In addition to these, there are also in the use of temporary electricity in the process of power line broken rectification before use, the risk of protection of pipe corridor welding, welding equipped with a fire catching basin and in the lower layer of the fireproof cloth for protection and so on, it is these strict safety management measures and continuous improvement, so that the company in the past year to achieve the goal of zero accidents, won the recognition of the Carlsberg Zero Accident Leadership Award.
This award is the result of the joint efforts of all construction staff and the project team, and the sense of responsibility is hidden in everyone's heart. By continuously improving the safety management system, introducing advanced technology, optimizing production process and other measures, not only has the goal of zero accident been achieved, but also promotes the development of the company's technological innovation. This honor is not only a high recognition of the company's technical engineering team, but also the highest praise for the company's persistent adherence to the concept of safety first and technological innovation. Today, the Carlsberg (Foshan) Beer Production Base Project is advancing the installation of equipment and preparing for the launch of trial production, which will be officially put into operation at the end of August.
We are confident that adhering to the sustainable development path of green, low-carbon and energy-saving will make the mountains where our customers are located more beautiful, the water clearer and the sky bluer, injecting strong vitality into industrial development and becoming a new flag-bearer in promoting the high-quality development of the local economy and society.
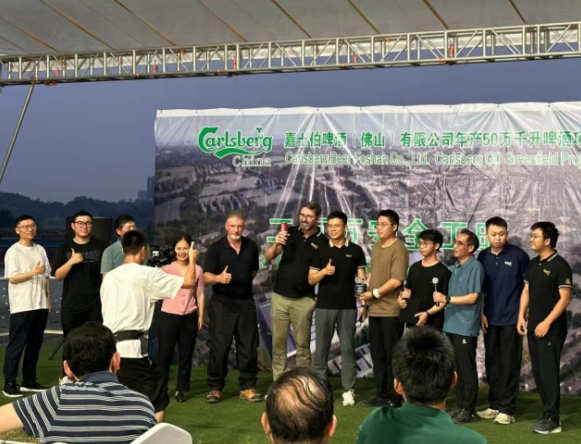
(Text/Engineering Center Chen Yangyang, Strategic Operation Department Zhang Hanlu)